DALLAS — Air travel is an engineering marvel, not only for the engines that lift an aircraft into the air, but also for the intricate systems that keep the cabin running smoothly and comfortably. Among the vital, behind-the-scenes systems is the drainage system, which regulates the drinking water supply and wastewater disposal during flight.
From coffee brewing in the galley to flushing toilets at 35,000 feet, the aircraft water and waste system is a hygienically designed, self-contained system that is clean and efficient from takeoff to landing. This article examines how this critical system operates, from water supply to waste drain, and what technology enables it.
The Potable Water System: Clean Water in the Sky
At the center of an aircraft's water system is the potable water system, which stores and provides clean water to lavatories, galley, and other service areas. The water must be of high sanitary quality and supplied in pressurized form at higher altitudes.
Key Elements
- Water Tanks: These tanks are located in the cargo compartment or beneath the cabin floor and hold hundreds of liters. For example, an Airbus A320 has approximately 200 liters of drinking water.
- Pressurization Systems: Because the tanks are beneath the outlets, water must be pumped up. Small planes use electric pumps, while larger planes use engine bleed air or air provided by an Auxiliary Power Unit (APU) to pressurize the system.
- Temperature heaters: Inline under-basin water heaters are installed to prevent freezing.
- Servicing Panel: Ground crews top off the tanks using a water servicing panel. The panel features fill valves, a quantity indicator, and an overflow line to prevent overfilling.
- Monitoring Sensors: They provide data to the Flight Attendant Panel (FAP), which allows the crew to monitor tank levels.
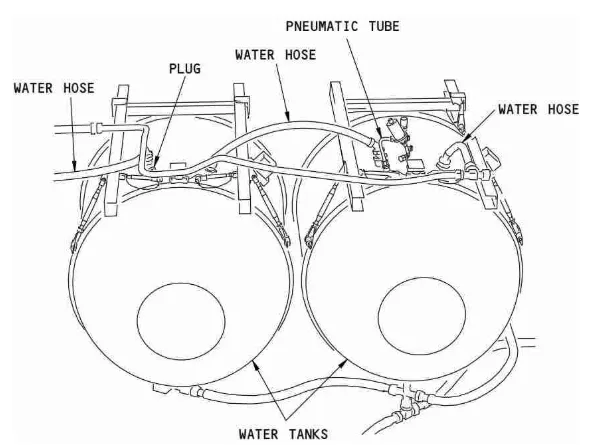
Usage of Water in the Cabin
Drinking water is used in:
- Hot/cold available bathroom sinks via a heater
- Galley faucets
- Some aircraft tea/coffee makers
- Drinking water, on the other hand, is typically served in bottles because of stricter health laws
Wastewater and Drainage: Clean Disposal in the Skies
Once utilized in the galleys, sinks, or lavatories, or lavatory waste flushed down, it must be hygienically discharged or held until the aircraft lands.
- Sink and Galley Drainage: Galley and washbasin waste water is overboard discharged by electrically anti-iced drain masts, which are installed under the aircraft fuselage. Two drain masts are commonly fitted, one for forward and one for aft waste water.
- Air Stop Valves: These only open when sufficient liquid has collected, preventing constant loss of cabin pressure down the drain lines. Pressure differential while flying helps evacuate wastewater, aided by gravity when the aircraft is on the ground.
- Toilet Drainage System: In comparison to residential toilets, aircraft lavatories utilize a vacuum toilet system that relies on differential pressure to draw waste through a closed waste tank, using minimal water for flushing.
Key Components:
- Flush Control Unit (FCU): Controls the actuation of the water and waste valves upon button press.
- Vacuum Generator: Used while on the ground to produce a vacuum for waste evacuation.
- Flush and Water Valves: Regulate the supply of the rinse water and the release of the waste.
- Waste Tank: Stores in-flight liquid and solid waste. For instance, an A320 contains a 170-liter waste tank.
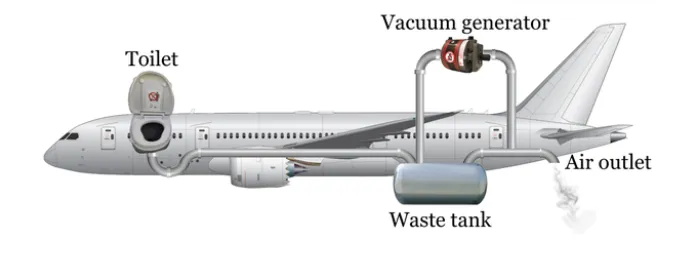
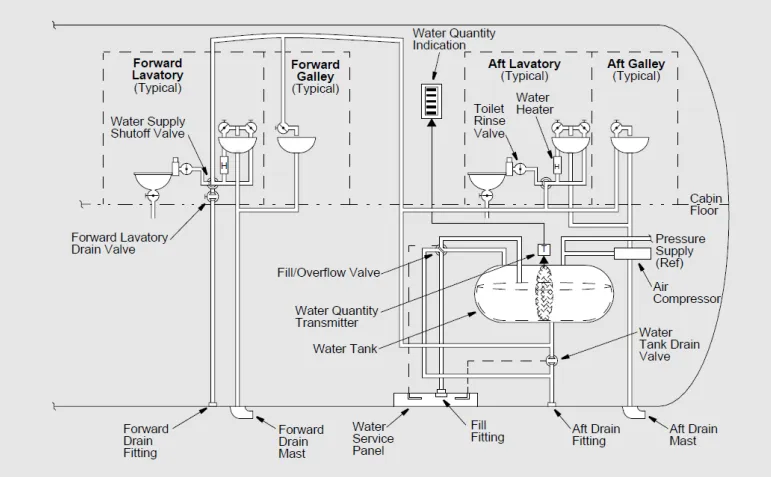
At a certain altitude, the vacuum effect is a natural result of the cabin's pressure differential compared to the atmosphere, making the generator obsolete during cruise flight (AN Aero).
Maintenance of the Systems on the Ground
Both waste and potable systems must be maintained periodically:
- Potable Water Servicing: A ‘Water Servicing Cart’ resupplies water through the aircraft's service panel. Tanks are filled to the level at which water overflows from the overfill drain line, i.e., to capacity. Maintenance staff periodically sample water tanks and disinfect water lines, and every airport is required to provide certified laboratory reports to confirm water quality.
- Waste Disposal: A ‘Lavatory Service Cart’ is used to empty the waste tank:
- A drain hose is attached to the toilet servicing panel
- The truck tank is loaded with waste drainage
- The tank is then rinsed out with a rinse hose, and the rinse water is drained as well
In smaller and older aircraft, recirculating toilets are used with the holding tank containing a blue disinfectant. The system recycles the flushing liquid, which is filtered between uses.
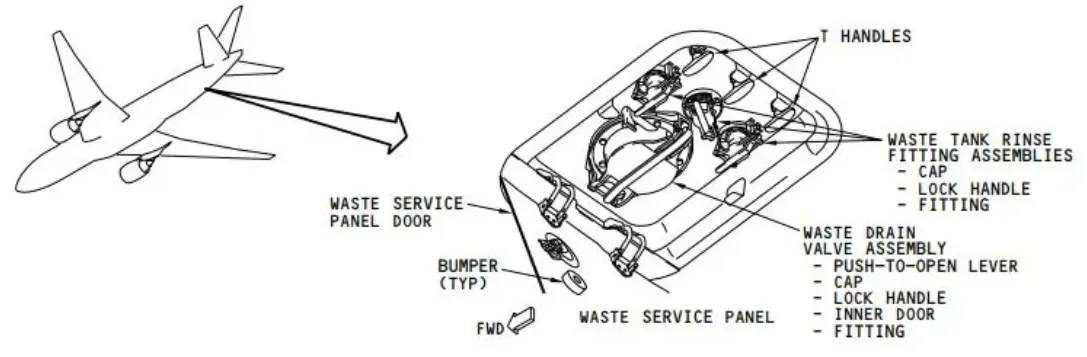
Common Issues, Safety Concerns
- Blue Ice: Leaks in the waste system, especially on older aircraft, can cause freezing fluid to accumulate on the fuselage. Broken apart while airborne, this ‘blue ice’ can result in:
- Fuselage damage
- Engine ingestion (especially on older tri-jet aircraft such as the Boeing 727)
- System Monitoring: New planes use computerized systems, which:
- Identifies faults
- Measures tank levels
- Sends notifications to central maintenance systems
Engineering Challenges and Innovations
Aircraft drainage systems have to deal with:
- Space and weight limitations
- High temperature and pressure gradients
- Health and safety law
To counter these, manufacturers are turning to:
- Lightweight materials
- Smart monitoring systems
- Eco-friendly plumbing designs
Simplifying Aircraft Waste, Water System Maintenance
Aircraft waste and water systems are undergoing a quiet revolution, with OEMs focusing on system reliability, maintainability, and weight savings. Traditionally, lavatory and galley water systems were maintenance nightmares, particularly in waste management. But new materials, design, and innovative diagnostics are making this critical area of aircraft maintenance simpler.
Potable systems require routine cleaning, decalcification, and periodic disinfection. Wastewater systems, particularly those that process "black water" from toilets and galley trash, face more extreme wear and tear from corrosive substances and foreign object damage. Sensors in this environment are more likely to fail and need more frequent inspection. The design of waste and water components is also changing.
According to a report by Aviation Week, modern aircraft, such as Cessna Citation jets, utilize optical sensors and "slingers" to prevent tanks from becoming contaminated. However, such sensors can malfunction if contaminated, sending false signals that shut down regular service. Corrosion, too, is a significant problem, often driven by chemicals used to treat waste.
To combat this, OEMs now use corrosion-resistant composite materials, which not only enhance durability but also extend the life of the product. Trays beneath tanks are being redesigned using plastic materials to minimize the threat of leaks.
These advances, although often unseen by passengers, are essential to reducing AOG events and maintenance man-hours, smoothing aircraft operations, and saving dollars.
Conclusion: Silent Heroes of Flight Comfort
While passengers might not appreciate it, the aircraft drainage system is paramount to delivering a clean, safe, and comfortable flight experience. From the potable water tank to the waste tank, each component is designed with efficiency in mind at altitude.
The aviation MRO marketplace is undergoing rapid change, driven by the intersection of digital technologies and predictive maintenance strategies. Aircraft interior systems, long the Cinderella of systems, are now at the center of innovation, as OEMs, airlines, and MRO providers utilize advanced data analytics, connectivity, and automation to optimize maintenance, enhance passenger comfort, and reduce operational costs.
Sophisticated cabins now often incorporate sensors and networked components that provide their status in real-time. Such a shift enables predictive maintenance, reducing unscheduled pulls and increasing the dispatch reliability of the aircraft.
For example, the introduction of "smart galleys," seat sensors that are integrated, and condition-based monitoring of lavatories, lighting, and inflight entertainment systems has changed the way airlines think about cabin health.
Several OEMs, such as Diehl Aviation, Collins Aerospace, and Safran, are making significant investments in wear, corrosion, blockage, and malfunction detection systems before these issues become significant problems. Airlines are similarly proactive in their operational strategies, employing AI-driven analytics software to analyze high volumes of aircraft health data and identify faults, facilitating rapid resolution.
As aircraft become more intelligent and sustainable, even such nuances are being optimized to help promote the greater goal of cleaner, safer flight.