DALLAS — Modern airliners are like flying data centres. They’re packed with thousands of sensors that constantly report engine status, fuel usage, and more. A Boeing 787 Dreamliner, for instance, generates on average 500 GB of system data every flight.
Airlines use this flood of live data to predict maintenance needs and optimise operations. Maintenance teams can spot and fix potential failures by crunching the sensor feeds with machine learning before a plane breaks down. The result is fewer delays, lower costs, and safer flights.
Thousands of sensors aboard today’s jets send “big data” to ground teams. Airlines use AI to analyse that data for maintenance and fuel-efficiency gains. Connected aircraft stream data via satellite and ground links to maintenance centres, allowing airlines to run predictive maintenance instead of just routine checks.
For example, General Electric (GE) jet engines log ~5,000 data points per second, and Airbus A380s can have 25,000 sensors per plane. All that info is downloaded on the ground so AI tools can learn patterns. If the AI sees a turbine vibration creep above normal, it can flag an alert long before a mechanical issue happens.
This means moving from “replace-it-just-in-case” schedules to fix-it-when-needed plans. Because fuel is so expensive (about 20–30% of an airline’s costs), airlines also feed aircraft performance and weather data into AI systems to optimise flight paths and save fuel. Even a 1% cut in fuel burn can save a carrier millions yearly.
Predictive Maintenance in Action
Using AI, airlines are turning maintenance from reactive to proactive. Instead of waiting for parts to fail, AI predicts faults. Mechanics get alerts like, “Replace part X in 50 flight hours.” This approach is already delivering big wins.
Let’s dive deep into how the big players today use AI to follow their fleet's skin-care (or maybe a full-body medical checkup) routine.
- Delta TechOps (USA): AI brings a change
Delta Air Lines (DL) has been a real trailblazer regarding AI-powered predictive maintenance. They use the APEX (Advanced Predictive Engine) system, which collects real-time engine data throughout flights and uses AI to analyse it. This helps Delta keep a close eye on engine health and plan maintenance visits exactly when needed; no more, no less.
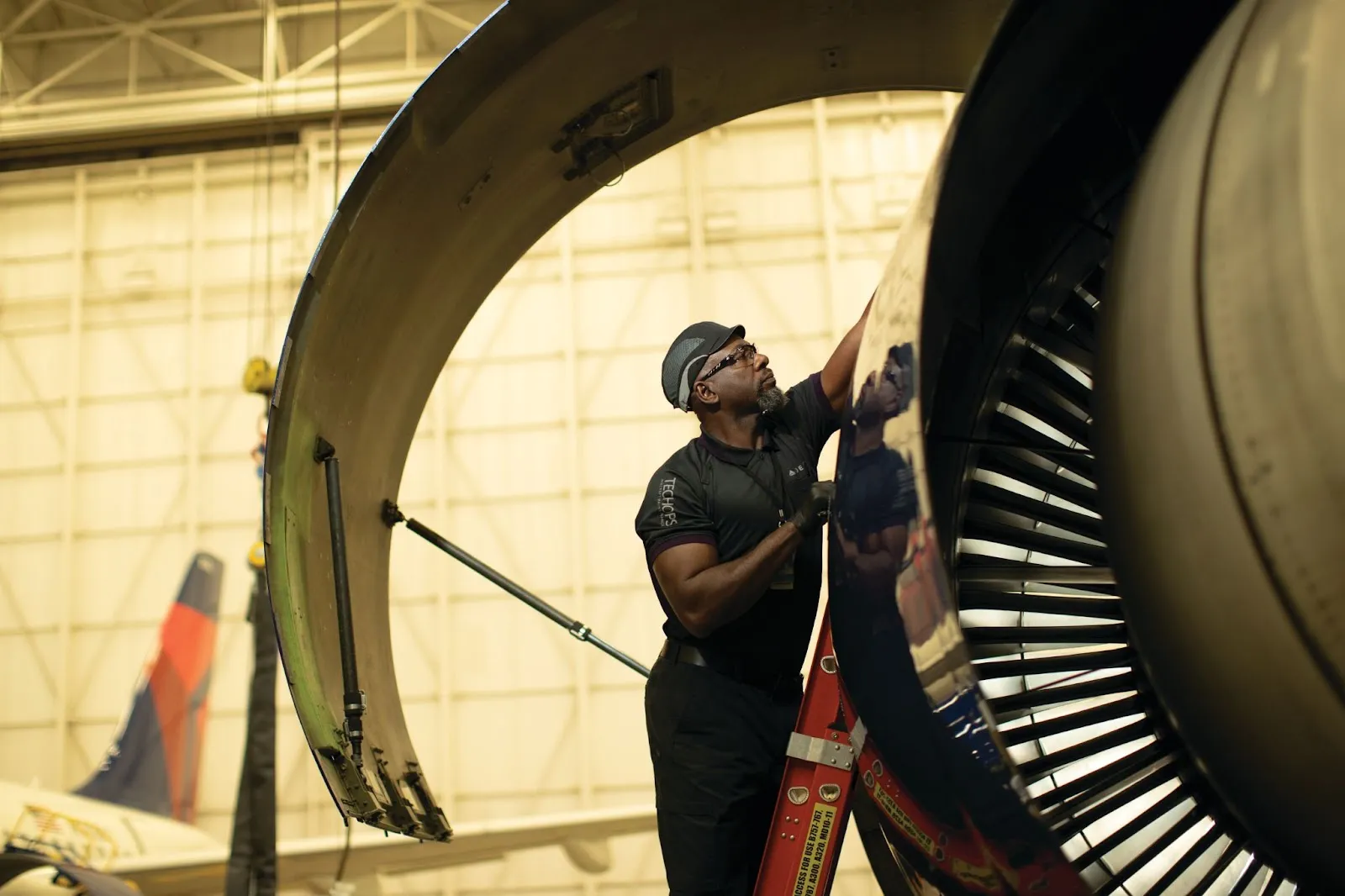
The results speak for themselves. From 2010 to 2018, Delta slashed its maintenance-related cancellations from a staggering 5,600 to just 55 annually. That’s about 100 times fewer breakdowns. Such a huge drop means smoother travel for passengers and massive cost savings for the airline. Delta says the APEX programme saves them eight figures every year. The tech’s impact was so significant that it won Aviation Week’s Innovation Award in 2024.
What stands out about APEX is how it combines AI with real-time data to predict failures well before they happen. Instead of fixing problems after a breakdown, maintenance teams get alerts like “replace this part within 50 flight hours,” allowing them to act proactively. This precision reduces unnecessary repairs, minimizes downtime, and boosts overall safety.
By turning maintenance from a reactive to a proactive task, Delta keeps its fleet flying reliably while cutting costs, which is a win-win for the airline and passengers alike. Impressive, right?
- Qantas (Australia): AI on the Frontlines of Flight Ops
Qantas (QF) has been leaning into AI not just for passenger experience or ticketing but also deep into flight operations and predictive maintenance. One major move? Partnering with Airbus to adopt the Skywise Predictive Maintenance platform (S.PM+). This system taps into real-time aircraft data to spot signs of wear and tear, helping engineers fix issues before they cause delays or in-flight failures.
With sensors spread across its fleet, particularly the Airbus A330s and newer aircraft, QF can now monitor performance and health metrics on the fly. If something’s off, say a temperature spike or abnormal vibration in an engine component, Skywise sends alerts to ground teams even before the aircraft lands. Maintenance crews inspect or replace parts proactively, cutting the risk of last-minute fixes.
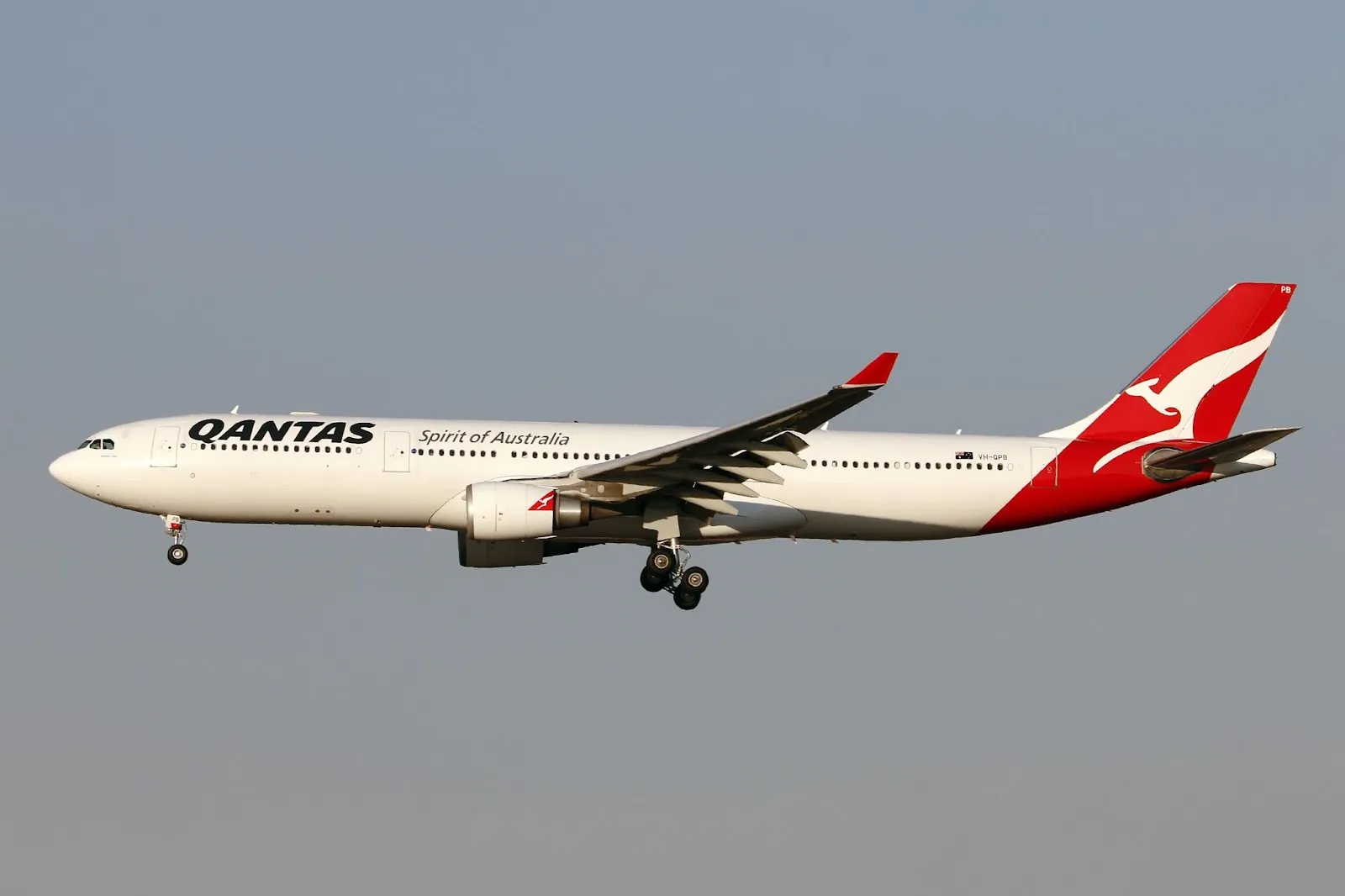
This tech has helped Qantas reduce unscheduled maintenance events and boost overall aircraft availability, especially during peak travel windows. It also plays a key role in managing the airline’s older jets until its next-gen fleet arrives.
They’re also using AI cleverly, through a custom “Constellation” tool designed to optimise flight routes by factoring in real-time weather data and aircraft performance. This system helps dispatchers adjust routes on the fly to save fuel and avoid bad weather, making flights more comfortable and punctual.
- Etihad Airways (Middle East): Turning Data Into Action
This was previously brought up when, back in early 2021, United Airlines (UA) partnered with Lufthansa (LH) group to bring the AVIATAR digital platform into its operations. The focus was on predictive maintenance for United’s Boeing 777s and Airbus A320s, with plans to expand to the 737 fleet. Together, they rolled out custom-built condition monitoring tools specifically designed for Boeing 737 NG and Airbus A319/A320 aircraft, giving maintenance teams a sharper view of potential issues before they became real problems.
Later that year, Etihad Airways (EY) signed an agreement with Lufthansa Technik to adopt parts of its AVIATAR digital operations suite. The aim was to sharpen its maintenance strategies using real-time data and analytics. But how did they do it?
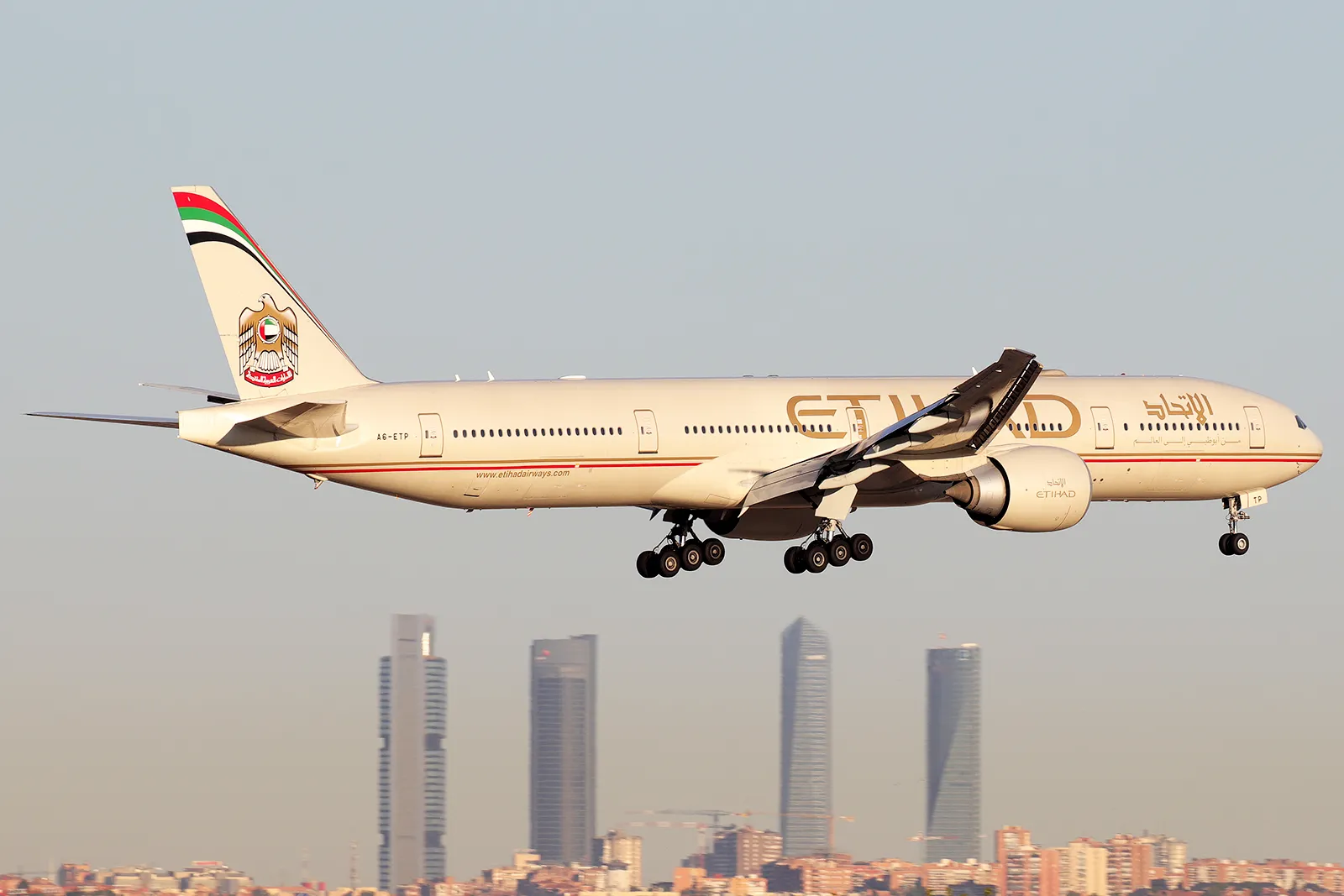
The partnership focused on three main tools: fuel analytics, condition monitoring, and automated line maintenance planning. These tools were designed to improve operational efficiency while cutting costs and delays.
Fuel analytics helped Etihad examine its fuel burn patterns. The AI system analysed flight data to spot unusual spikes or inefficiencies, separating them from things like wind or reroutes. That way, engineers could pinpoint technical issues early and take action to reduce unnecessary fuel consumption.
Condition monitoring gave the airline a live view of its aircraft health. Fault messages, flight logs, and maintenance records were all fed into one platform, so the team could track what parts were under stress and schedule checks or replacements before something went wrong. It was a big step forward in avoiding last-minute disruptions.
Etihad also used automated maintenance planning to adapt to fast-changing schedules. Instead of relying on static spreadsheets, their system automatically adjusted line maintenance tasks based on flight activity, reducing downtime and keeping aircraft in the air longer.
Together, these tools laid the groundwork for Etihad’s shift toward more innovative, more proactive maintenance. It wasn’t just about reacting faster; it was about making better decisions using data, which still shapes how the airline manages its fleet today.
- Air France–KLM and Google Cloud: Speeding Up Maintenance Insights with AI
Air France (AF)–KLM (KL) has pioneered using data for aircraft maintenance for quite some time. According to AF, their in-house tool, Prognos, which dates back to the early 2000s, has become a popular choice, with over 80 airlines worldwide relying on it for predictive maintenance. It helps airlines spot potential issues before they happen, reducing the chance of unexpected breakdowns.
But they didn’t stop there. Air France–KLM recently teamed up with Google Cloud to take things further. With this partnership, they started analysing all their flight and maintenance data using AI-powered tools. The biggest win? What used to take hours of maintenance analysis can now be done in just minutes. This speed boost means the airline can spot problems faster, fix them before they turn serious, and keep flights on schedule more reliably.
Faster insights don’t just improve reliability; they also help cut down waste. Maintenance teams no longer spend time chasing down non-issues or performing unnecessary checks. Instead, they focus their efforts exactly where they’re needed. That’s good news for the airline’s budget and passengers who hate delays.
Plus, by being more efficient with maintenance and operations, Air France–KLM also supports environmental goals. Less wasted time on the ground and fewer unplanned repairs mean lower fuel consumption and reduced CO₂ emissions. It’s a solid example of how AI and cloud computing are helping make aviation smarter and greener.
Digital Twins and Smarter Fleet Management
Beyond single sensor alerts, airlines are building digital twins – virtual copies of aircraft and engines fed by live data. Rolls-Royce, for example, launched its IntelligentEngine digital twin program in 2018 to predict engine part wear and remaining life with AI.
In practice, an engine’s sensor stream is mirrored in software; AI models then run “what-if” simulations. Lufthansa Technik describes a similar vision: feed the MRO shop the real-time health of an aircraft so that “using AI, [it] can predict failure and advise the operator on which actions to take and when.” In other words, digital twins let airlines test fixes virtually and fine-tune maintenance timing.
Machine learning also helps manage the entire fleet. Airlines use AI to forecast when each aeroplane will need work to rotate spares and schedule hangar time smoothly. Some carriers are even exploring AI-driven inspections: drones with computer vision can scan fuselages and engines for cracks, reducing manual inspection time. AI in fleet management means longer aircraft lifetimes and fewer last-minute equipment swaps.
Efficiency, Costs, Sustainability
The benefits of AI-driven maintenance spill over into cost-cutting and greener operations. Predicting failures ahead of time slashes costly AOG delays and spare-part overruns. It also means carrying fewer parts on every flight (saving weight and fuel). AI is also used on the flight deck: eco-piloting tools help pilots choose optimal altitudes and speeds based on AI analysis of weather and traffic, reducing fuel burn. In one instance, Alaska Airlines (AS) used an AI route optimiser to trim 480,000 gallons of jet fuel in six months. Minor improvements add up fast when fuel costs tens of millions per carrier.
Airlines also use AI to improve loading and routing: for example, algorithms predict how many bags and meals to load or which alternate routes save time. The bottom line is smoother operations.
Fewer unplanned maintenance events mean fewer passenger mishaps, and as a bonus, AI data tools can help cut ground time for each aircraft by up to 5–10%. That reduces staffing and fuel costs on the ground as well. All these efficiencies improve the airline’s bottom line and support environmental goals: lower fuel use means lower CO₂ emissions per flight.
What’s more, AI supports more innovative inventory management. Airlines don’t need to stock every part at every hub anymore; machine learning predicts part demand based on usage trends and fleet cycles, making supply chains leaner and cheaper. And then there’s aircraft washing; even something as basic as that is going smart. Some carriers now use AI to optimise the timing of engine and fuselage washes, which helps maintain aerodynamics and improves fuel efficiency without wasting resources.
As sustainability targets get stricter, AI is helping airlines meet them. By avoiding unnecessary delays, improving aircraft health, and fine-tuning every trip to the last detail, carriers prove that profitability and sustainability can fly side-by-side.
Looking Ahead: Challenges and Change
Of course, turning all this data into reliable predictions isn’t exactly plug-and-play. The biggest headache? Getting shiny new AI systems to fit into decades-old maintenance routines. It’s like trying to teach your grandpa to use TikTok; it takes patience, training, and convincing.
Crews need proper training, companies must build solid data pipelines, and cybersecurity can’t be an afterthought. Plus, there’s the classic “Who owns the data?” drama, with aircraft makers, airlines, and MROs each holding pieces of the puzzle.
But the industry seems optimistic. The trend is moving toward more data sharing, thanks to platforms like Airbus’s Skywise and GE’s Predix, paired with more innovative analytics tools that help make sense of it all.
Despite these bumps, AI’s role in maintenance is only growing. Success stories from Delta, Lufthansa Technik, Air France–KLM, and others point the way forward. In the next few years, expect even deeper use of AI and machine learning; imagine fully automated inspections and digital twins keeping tabs on entire fleets in real time.
This future means fewer delays, lower costs, and safer airline skies. By spotting issues before they ground planes, AI isn’t just making flying smarter; it’s making it cleaner and more reliable, too. And honestly, who doesn’t want a smoother flight and fewer surprises?