DALLAS — To the lay observer, it may not appear comforting to see a wing flex in flight, but this bending is a vital safety mechanism.
By no means are wings rigid; they are designed to bend under aerodynamic loads, to absorb energy and prevent structural collapse. Whether encountering turbulence or taking off, modern wings endure immense stress while remaining intact.
All this is made possible by sophisticated materials, rigorous testing, and conservative design margins. From early metal construction to modern carbon composites, wings have evolved into high-performance structures that quietly absorb immense aerodynamic forces in flight, ensuring every flight is safe and efficient.
Comprehending Flight Wing Loads
The Role of Wing Loading
Wing loading plays a significant role in an aircraft's performance, and it is calculated by dividing the aircraft's weight by its wing area. For small aircraft like the Cessna 172 (with a wing loading of about 13 lb/ft²), which can take off from short airstrips with pleasant handling qualities, low wing loading improves maneuverability and decreases stall speeds.
However, the more wing-loaded aircraft (above 100 lb/ft²), such as the Airbus A350, require longer runways for their long-haul efficiency and higher cruising speeds. This is the compromise managed by the designers to some extent, where they trade fuel efficiency, strength, and aerodynamic lift.
G-Forces and Structural Load Limits
Wings of an aircraft are designed to withstand dynamic loads greater than those encountered in level flight. In unstable or sudden maneuvers, G-forces or vertical acceleration can briefly increase. Commercial aircraft, under regulations by the likes of the FAA and EASA, need to generally be able to withstand at least +2.5g and -1.0g.
Wings do need to endure the "ultimate load" at certification, which is 1.5 times the "limit load," to ensure safety in extreme and exceptional conditions, such as steep maneuvers or strong gusts. This inherent strength enables aircraft to withstand structural loads under a variety of flight conditions, converting passenger turbulence into a safe journey by design.
Why Wings Bend: A Guide to Wing Flexibility
Rigidity vs. Elasticity
Wings are designed to bend, not remain rigid. Due to their flexibility, they can dissipate energy and absorb aerodynamic loads without exerting excessive stress on the fuselage or control structures; however, excessive flex results in failure, posing threats such as oscillatory instability and flutter.
Engineers employ aerodynamic shaping, mass-balanced distribution, and internal dampers to avoid this and ensure a stable response across the flight envelope. This strength-elasticity trade-off is directed by advanced simulation and wind tunnel testing to produce wings that transition smoothly to in-flight conditions.
Real-Life Wing Flex Examples
Modern composite aircraft, such as the Boeing 787 and Airbus A350, are excellent demonstrations of wing flexibility, with wings that bend upwards by up to 25 feet when in flight. This radical curve is all intentional. Carbon fiber composites enable the selective application of stiffness, supporting areas that require it while allowing movement elsewhere.
NASA testing and in-flight video confirm that this flex more evenly distributes aerodynamic loads, offering enhanced passenger comfort during turbulence. Far from a structural flaw, wing flex is an essential safety and performance enhancement, quietly delivering smoother, more resilient flight.
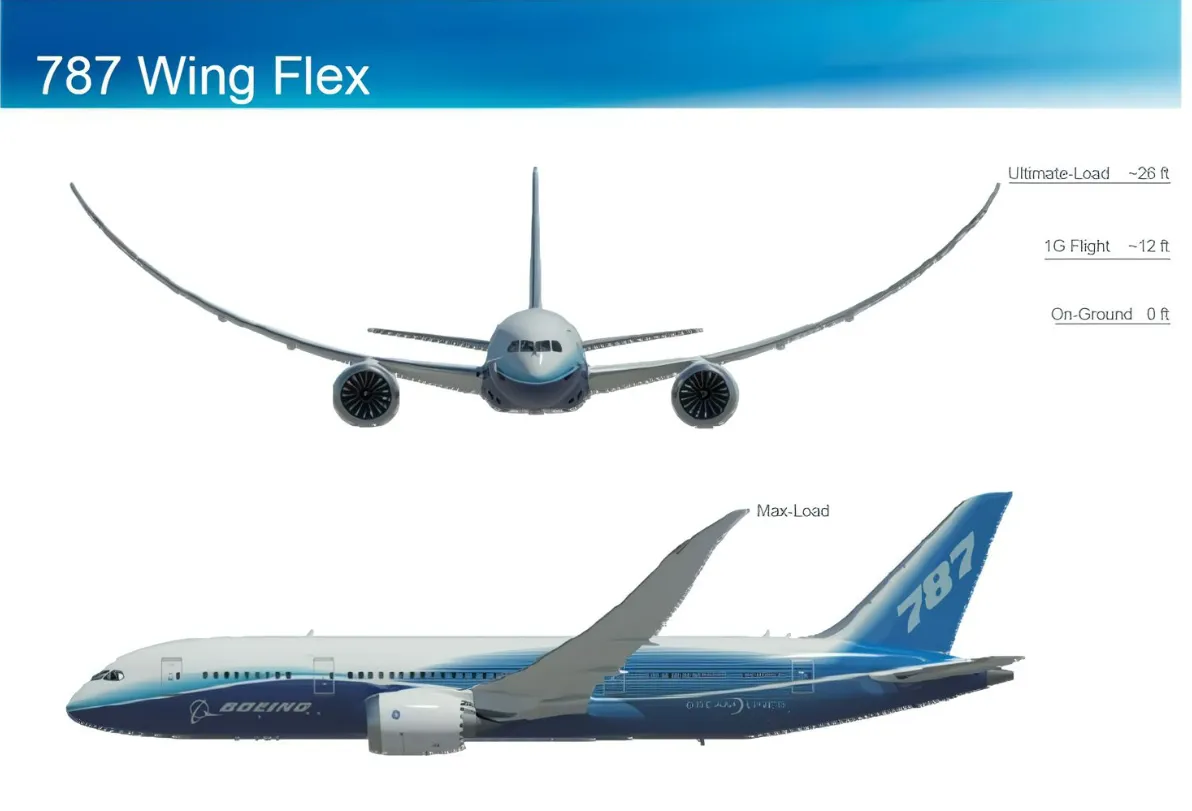
Comparison of Contemporary Composite Wings with Traditional Aluminum Wings
Evolution of Wing Material
Wings have undergone significant changes over the last century. Due to their strength-to-weight ratio, aluminum alloys were used in early aircraft, such as the Boeing 707 and Airbus A300. Since thousands of rivets were used to construct these wings, fatigue and corrosion had to be controlled through regular inspections.
More recent aircraft, such as the Airbus A350 and Boeing 787, employ carbon fiber-reinforced polymers (CFRP), which enable engineers to design smoother aerodynamic surfaces with fewer joints and reduced weight.
Advantages of Composite Wings
CFRP wings possess impressive advantages. When they are loaded, they bend efficiently, which reduces stress and improves turbulence response. Extended maintenance is minimized through their resistance to corrosion and fatigue, particularly in seashore or wet environments.
Through improved lift-to-drag ratios, the curved CFRP wings of the 787 enhance fuel economy. The composites also simplify the production of complex features such as raked wingtips compared to metal.
Composites-Related Engineering Challenges
Composites have their disadvantages, including the need for lightning protection to be integrated and the challenge of detecting the interior damage. They require costly autoclaves, long curing times, and precision quality control for their fabrication.
Despite the obstacles, composites are an integral part of modern wing construction, given the long-term gains in performance.
Ground Testing: Challenging the Limits of Wings
Static Load Testing
Static testing verifies structural safety through the simulation of 150% of the peak aerodynamic load. Boeing's 777X wing was bent over 30 feet forward during ultimate load testing in 2019, demonstrating the margin built into its composite structure.
Fatigue Testing
Full-scale fatigue tests utilize hydraulic rigs to cycle wings through mock takeoffs and landings, simulating flight stresses over decades in a matter of months. These tests verify the aircraft's Design Service Goal (DSG), revealing micro cracks or delamination.
Aeroelastic Testing and Flutter
To ensure oscillations remain within safe limits for all speeds, flutter is assessed with ground vibration tests and flight testing.
In-Flight Monitoring and Wing Performance
Real-Time Load Sensors
There are now embedded strain gauges and wing structural health monitoring systems built into new jets. They monitor bending, torsion, and vibration in real-time, enabling both on-the-spot safety checks and proactive maintenance. Data collected after flights is reviewed by airlines to track patterns of fatigue and plan ahead-of-time inspections.
Fly-by-Wire's Role in Wing Load Management
This system reduces wing stress by electronically counteracting control surfaces during gusts or turbulence. Load alleviation systems onboard aircraft, such as the A350 and 787, automatically deflect control surfaces to minimize structural stress, thereby enhancing ride comfort and extending airframe life.
Safety and Regulatory Standards
Certification Qualifications
For Type Certification, producers must demonstrate that wing structures meet the stringent criteria for integrity as specified in CS-25 (EASA) and FAR Part 25 (FAA). Compliance involves conducting fatigue, dynamic, and static tests on full-scale assemblies, while regulatory inspections ensure that safety margins are met through physical demonstrations and proof of data.
Open Protests, Openness
Producers regularly make wing tests public in an attempt to encourage transparency and trust. Besides demonstrating engineering proficiency, historical testing, such as Boeing's 777 wing flex test, helps provide reassurance to the public, airlines, and regulators regarding the structural integrity and certification of the airframe.
Case Studies
- The Boeing 787’s entire composite wing was observed to extend as long as 25 feet during flight. This flexibility enhances cabin comfort, minimizes fuselage stress, and enhances turbulence absorption. The carbon fiber's resistance to fatigue benefits operators with smoother flights and reduced maintenance.
- Airbus A350: Carbon fiber spars and adaptive control surfaces are employed to control aerodynamic loads. The A350 is stronger, lighter, and more fuel-efficient than the A330's aluminum wing, which is particularly significant on ultra-long-haul routes.
- The largest composite wings in service, measuring 235 feet and with foldable tips, are on the Boeing 777X. Design strengthening was prompted by a 2019 static test failure at 99% load, highlighting the need for strict certification standards.
Next-Generation Wing Structures: Future Trends
Morphing wings are gaining popularity as aviation seeks greater sustainability and efficiency. Wings with flexible skins and internal actuators can alter shape during flight, replacing traditional hinged flaps and reducing drag, noise, and mechanical complexity. This concept is demonstrated through NASA's ACTE and SABER research projects. Achieving this would involve using materials such as shape-memory alloys and smart composites.
To reduce the environmental impact, recyclable thermoplastics are being explored in parallel. Real-time monitoring of stress and damage enables condition-based maintenance through the use of embedded sensors and artificial intelligence-based structural health monitoring systems. Digital twins coupled with adaptive wings could one day dynamically optimize safety and performance on every flight.
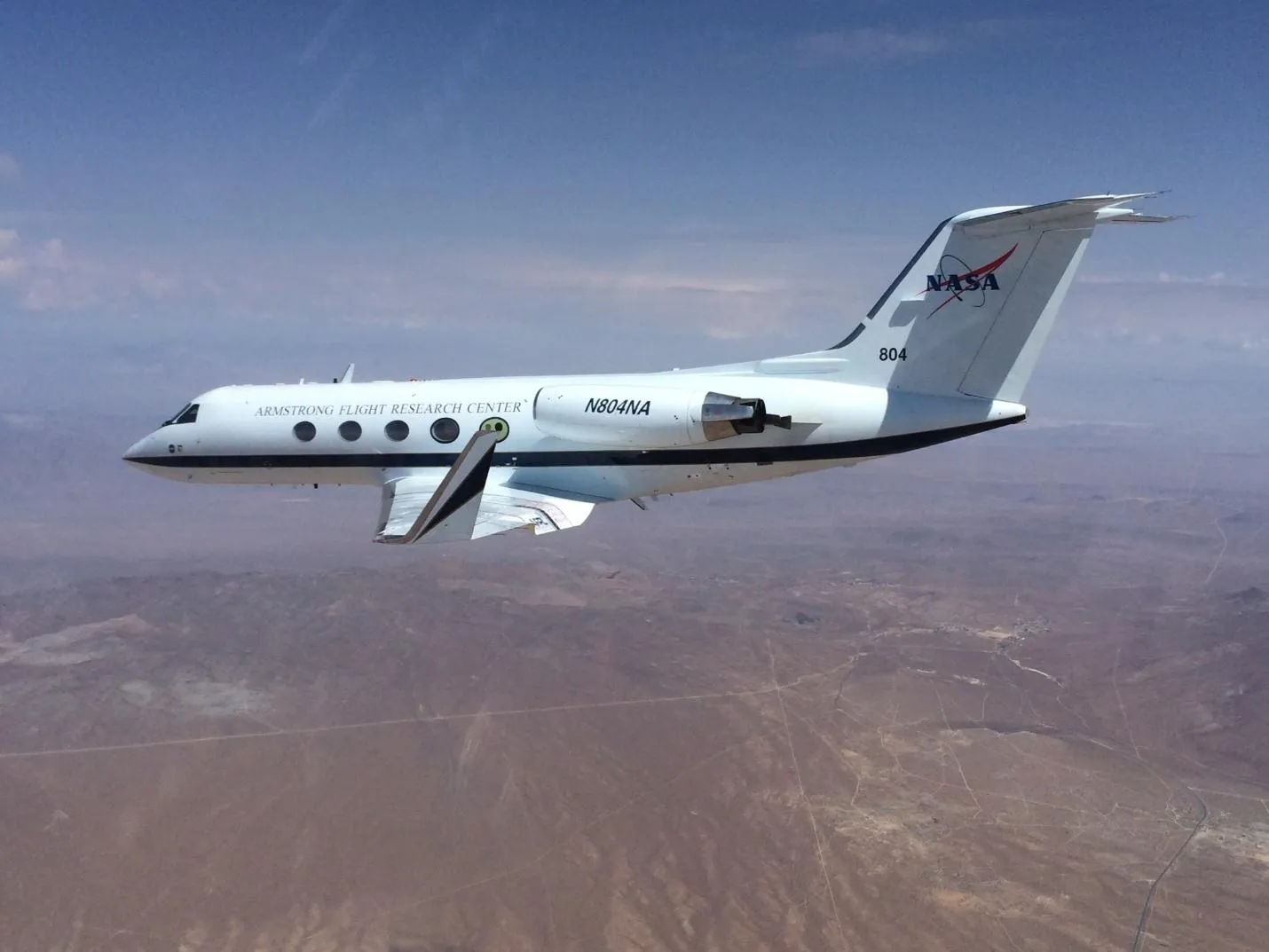
Conclusion: The Art and Science of the Bending Wing
What appears to be an unsafe wing flex is a sophisticated technical feature. Rather than a defect, it improves efficiency, safety, and helps to redirect aerodynamic forces.
Modern wings, made from materials ranging from rigid aluminum to flexible composites, demonstrate that aircraft design has evolved from rigid structures to ones that bend and flex. Every curve and flex is a calculated response, representing the art of perfect flight.