DALLAS — Far above the planet, at cruising altitudes of 35,000 feet, the conditions outside a modern airliner are those of intense cold, thin air, and potentially lethal atmospheric pressure.
As people within the cabin enjoy their meal or movie, the conditions outside the windows are hostile to human existence. The air pressure is reduced to approximately 3.5 psi at this altitude, compared to about 14.7 psi at sea level. Individuals would suffer rapidly within minutes of hypoxia, or insufficient oxygen, in unpressurized environments. Prolonged exposure can lead to decompression sickness, loss of consciousness, and death.
Still, under this adverse environment, contemporary commercial airplanes provide safe and comfortable cabin conditions. This is achieved through advanced pressurization systems that control the air pressure within the fuselage, maintaining a comfortable altitude of approximately 6,000 to 8,000 feet.
The technology behind such systems is the backbone of commercial flight, ensuring passenger wellness and comfort despite the structural and operational constraints of the aircraft.
Why Aircraft Need Pressurization
- The Basics of Air Pressure and Altitude
Atmospheric pressure decreases with altitude because the weight of air above is less. Sea-level atmospheric pressure is what forces oxygen into the lungs. At 35,000 feet, however, oxygen partial pressure is too low to sustain human life, even though oxygen makes up about 21% of air. To address this, airplane cabins are pressurized to mimic lower elevations, usually around 8,000 feet. Current jets, such as the Boeing 787 and Airbus A350, enhance this with 6,000-foot cabin altitudes, thereby minimizing fatigue on long journeys. Without pressurization, breathing and contemporary air travel would not be possible.
- How Pressurized Cabins began
Traveling comfortably in a pressurized vessel became possible with the introduction and innovation of cabin pressurization. Such a system was never imagined to exist, but it revolutionized air travel. Before pressurization, aircraft could not operate at altitudes higher than 10,000 feet due to a lack of oxygen; hence, they were exposed to harsh weather, climate, turbulence, and drag.
This aspect arrived with the Boeing 307 Stratoliner in 1938, the first commercially available pressurized cabin airliner. Evolved from the B-17, it possessed an 11,000-foot cabin altitude at 20,000 feet. Although only a handful were built, it set an important precedent, enabling long-distance flight and establishing the quiet revolution that paved the way for air travel worldwide.
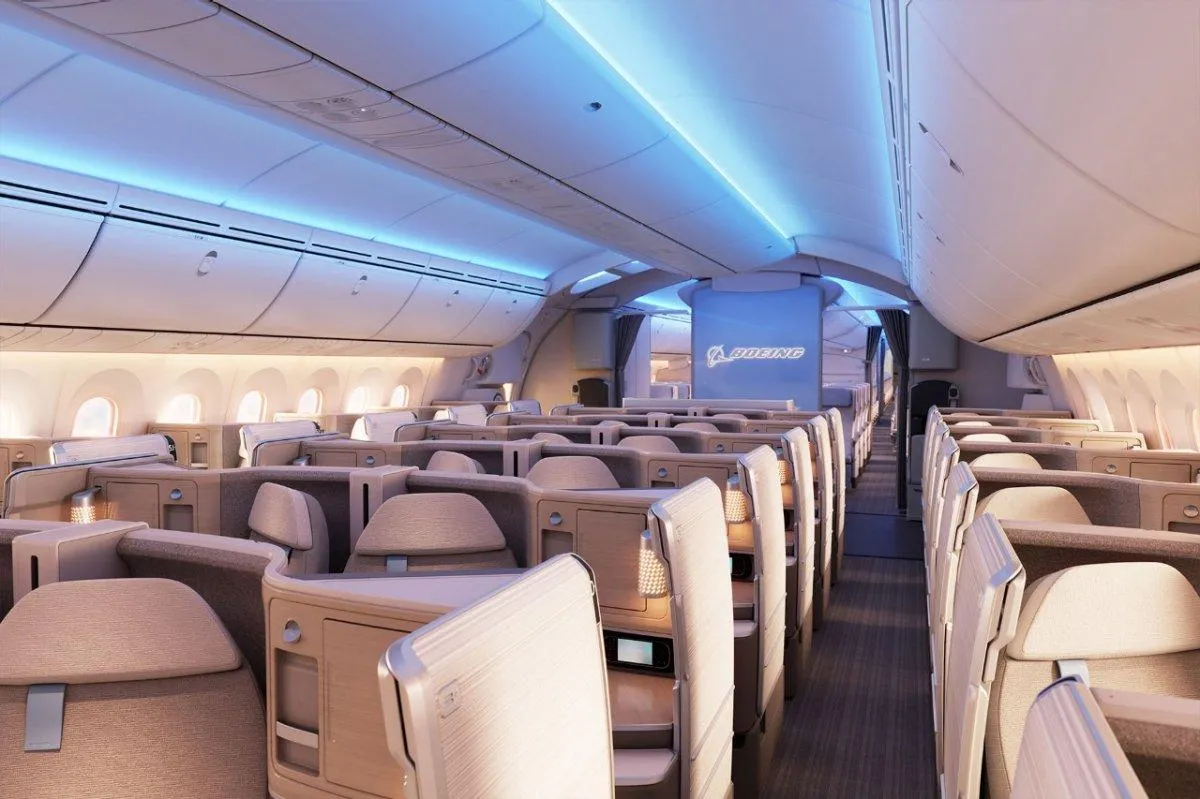
Working Principle
Creating a pressurized environment in an aircraft is no easy task, but rather a series of complex valves and components work in harmony to achieve this feat. Such a system is designed and used to ensure the safe operation of both passengers onboard and the aircraft itself in terms of structural integrity. When an aircraft pressurizes and depressurizes, immense and high cyclic loads are applied to the structure; therefore, periodic inspections are conducted.
The cabin pressurization system combines bleed air from the engine with environmental controls, such as humidity control and an Ozone detector, and automatic control valves that open and close upon landing.
- The Function of Bleed Air
Behind most contemporary pressurization systems lies bleed air, high-pressure air drawn from the compressor stages of the aircraft engines. The air is cooled and conditioned by the Environmental Control System (ECS) before being introduced to the cabin, ensuring a comfortable temperature and humidity for passengers. The ongoing inflow of compressed air continuously replenishes the cabin air, sustaining oxygen levels and managing cabin altitude during flight.
Certain next-generation airplanes, such as the Boeing 787, utilize electrically powered compressors rather than engine bleed air. This "bleed-less" configuration minimizes fuel usage and maximizes operational efficiency.
- Outflow Valves: The Unsung Heroes
Outflow valves regulate the flow of fresh air into the cabin to maintain the pre-selected cabin altitude set by the pilot. These valves are located in the aft fuselage, where they automatically open and close in response to the cabin pressure controllers.
Live data is fed into the computers from pressure sensors attached to the valves, which depict movement and adjust valve positions through electric and pneumatic actuators. Such a system is often referred to as a closed-loop system, ensuring safety and control rather than relying on external factors that could cause a mishap.
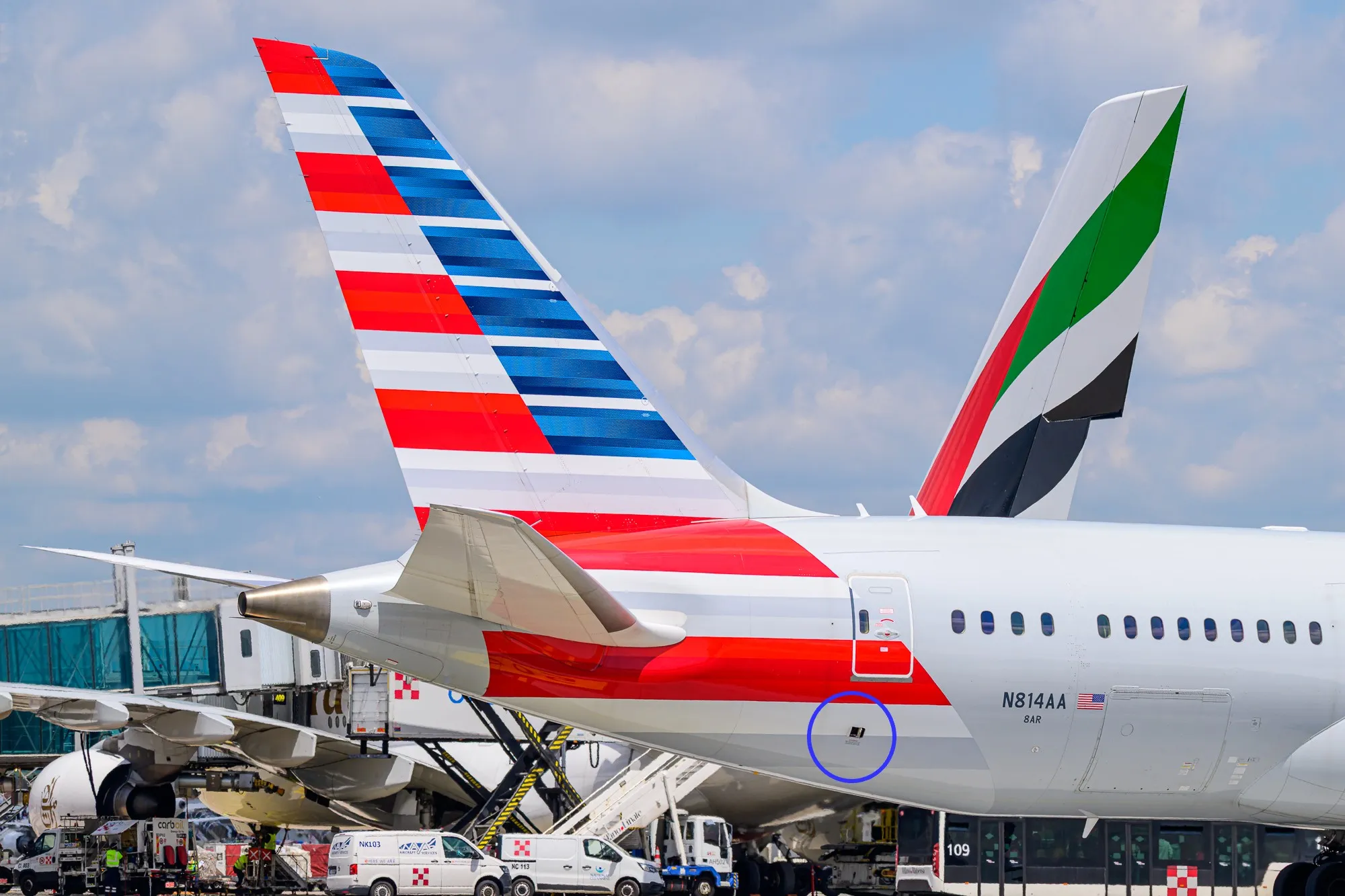
- Controllers and Altitude Profiles
Aircraft are required to climb and descend gradually to prevent a sudden loss of pressure differential. A rate of pressure change, between 300 and 500 ft/min, is often selected. Next-generation airliners, such as the Airbus A350, have a reduced cabin altitude, typically around 6,000 feet, compared to the traditional 8,000 feet, which enhances passenger comfort and reduces fatigue. Maintaining a balance between comfort and the structural load on the fuselage is a fundamental engineering challenge, requiring sound design and rigorous control.
Impact on Structure
Pressurizing an aircraft cabin involves more than simply blowing air in and maintaining oxygen, air conditioning, and humidity levels. It is a very complex system that also impacts the aircraft fuselage. High cyclic loads impact the aircraft during landing and takeoff due to pressurization cycles. Hence, aircraft maintenance engineers often inspect and assess the aircraft structure for any cracks or damage resulting from cyclic loads.
- Cabin Pressure Differential
The most important one is the cabin pressure differential, the difference between the pressurized air within the fuselage and the outside atmosphere at lower pressure. For the majority of aluminum-construction aircraft, this differential will be at its highest around 8.5 psi at cruise altitude. Composite structures and materials can withstand a higher pressure differential, which allows for a lower cabin altitude profile.
To withstand such stresses, the fuselage is designed as a cylindrical vessel that is pressurized during flight. The outside pressure is almost negligible, while the cabin pressure is greater. Such a design distributes stresses and loads symmetrically throughout the structure, resulting in a lower likelihood of fatigue cracks and damage. Hence, windows are rounded from the edge to avoid sharp corners where cracks could propagate and stress could be concentrated.
Regular NDT (Non-Destructive Testing) inspections are often performed during C and D checks, which ensure the early identification of any potential fatigue cracks.
- Composite on Modern Aircraft
Modern aircraft, such as the Boeing 787 and Airbus A350, incorporate high-grade composite materials, including carbon fiber-reinforced polymer, for the majority of their structure. These are lighter, stronger, and more resistant to fatigue and corrosion than aluminum. A major passenger advantage is the ability to maintain lower cabin altitudes, typically around 6,000 feet, which enhances humidity and reduces fatigue during long flights. Their higher fatigue resistance also increases airframe life, enabling manufacturers to upgrade both passenger comfort and long-term operational efficiency.
What Is the Consequence of Pressurization Failure?
Although pressurization systems are highly advanced, occasional failures can occur, although these are extremely rare. Planes are pre-programmed with various safety measures to safeguard passengers and crew in the event of such a failure.
- Gradual vs. Explosive Decompression
Decompression accidents are either gradual or explosive. Gradual leaks or defective seals can cause gradual decompression, which may go unnoticed until cockpit warnings appear. Explosive decompression is an abrupt phenomenon, usually resulting from structural failure, such as a burst fuselage or window, leading to a sudden pressure loss, tremendous noise, and condensation fog.
With no supplemental oxygen, passengers can become hypoxic, which causes confusion, impaired judgment, and loss of consciousness. The Time of Useful Consciousness (TUC) decreases with increasing altitude, approximately 20 to 30 seconds at 35,000 feet, up to several minutes at lower flight levels.
- Emergency Oxygen Systems
During any decompression, oxygen masks automatically drop down from the ceiling panels. The masks use chemical oxygen generators, which become active when the passenger pulls the mask to their face. These generators give 12–20 minutes of oxygen, sufficient time to bring the plane down to a breathable altitude.
Flight crews have more advanced systems, utilizing high-pressure oxygen bottles and positive-pressure masks to preserve cognitive function in cases of high-altitude emergencies. Governmental agencies such as the FAA and EASA require oxygen supplies following the aircraft's certified ceiling and flight profile.
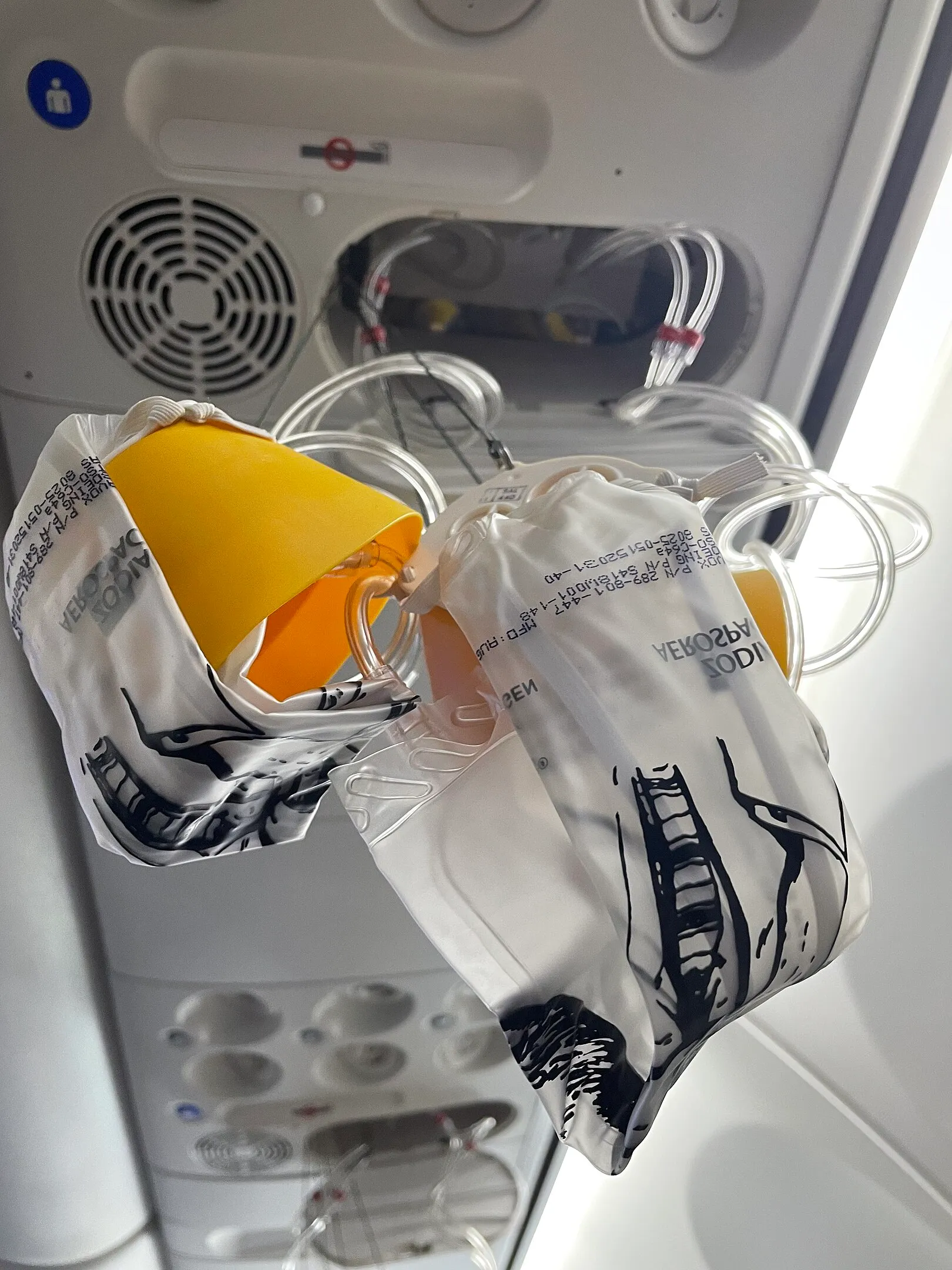
- Emergency Descent Protocols
Upon decompression, pilots undertake an emergency descent, generally to 10,000 feet as quickly as possible, at which altitude supplemental oxygen is no longer necessary. Rates of descent may range from 3,000 to 6,000 feet per minute, depending on air traffic conditions and terrain.
Modern aircraft systems are highly automated, with pressure valves, engine thrust, alarm systems, and other components working simultaneously to adjust pressure according to altitude. All of this is done in sync with each other to provide passengers with the utmost safety and protection, allowing pilots to focus on other onboard systems. Pilots undergo training in which they simulate a depressurization event onboard.
Incidents due to Pressurization Failure
Pressurization systems, despite being remarkably safe and reliable, can malfunction. A few incidents have occurred in history due to rapid depressurization mid-flight, and such incidents have shaped the pilot and engineering industries today.
- Helios Airways Flight 522
Perhaps the most dismal pressurization incident was Helios Airways Flight 522 in 2005. The Boeing 737-300 left Larnaca, Cyprus, with the pressurization system inadvertently left in manual mode after maintenance. As the plane ascended, there was a gradual decompression, but warnings were mistakenly read by the crew, resulting in hypoxia and incapacitation of both pilots and the majority of passengers. The plane operated on autopilot until fuel depletion.
This accident precipitated worldwide changes in checklist protocols, required pressurization cross-checks, and enhanced alert systems to prevent such accidents from happening again.
- Payne Stewart Learjet Incident
When professional golfer Payne Stewart's Learjet took off in 1999, a suspected pressurization problem was reported. Before the jet finally ran out of fuel and crashed, it continued to fly on autopilot across numerous U.S. states as the flight crew likely died from hypoxia. Due to the Payne Stewart tragedy, which exposed flaws in general aviation pressurization protocols, the business aviation sector has placed a renewed emphasis on inspecting and training emergency oxygen systems.
- Similar Incident
An Aloha Airlines flight 243 suffered a major structural breach in 1988 due to metal fatigue that ripped a section of the forward fuselage right off the heads of the passengers. This incident is often used as a case study to warn and govern modern engineering standards in the aviation industry.
The above incidents have directly influenced several changes being made and followed today in terms of design, pilot procedures, safety protocols, preventive maintenance, and more.
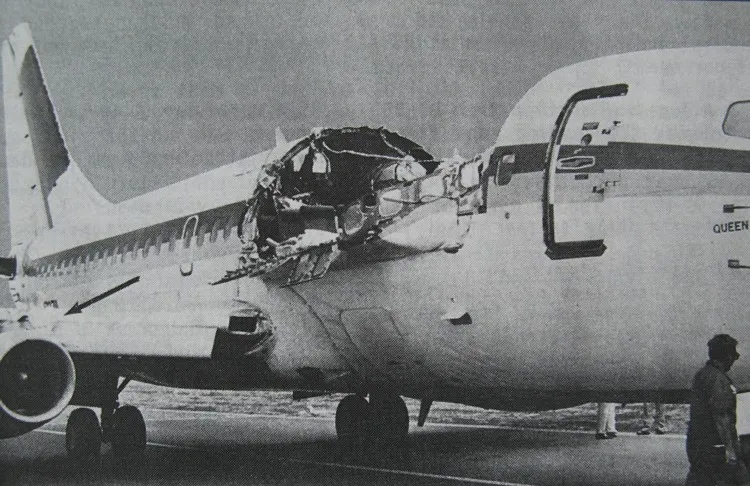
The Future of Cabin Pressurization
With the evolution of passenger expectations, the future of cabin pressurization lies in creating a cabin that is both safer and more comfortable. The Boeing 787 and Airbus A350 next-generation planes already have lower cabin altitudes of approximately 6,000 feet, compared to the older 8,000-foot standard. This reduces the symptoms of fatigue, Dehydration, and Jet lag
Improving digital pressurization systems also supports smarter, more responsive pressurization management with:
- Automatic reversion modes and predictive algorithms
- Ideas such as variable pressurization profiles for tailored comfort
In the future, new carbon fiber composites will be able to accommodate higher pressure differences safely. Along with predictive maintenance and Structural Health Monitoring Systems (SHMS), future aircraft will provide healthier, quieter, and more individualized flying experiences.
Conclusion
Pressurization of cabins is a subtle yet vital aspect of contemporary aviation, enabling safe and comfortable flight at high altitudes. Modern systems in use today are all automated and highly reliable, with multiple redundancies onboard. The cabin pressurization topic has been a trial-and-error method for generations, where engineers and designers have always learned from failure and continue to do so.
With limited knowledge and interest, passengers can feel secure on modern airliners, where a great deal goes on behind the scenes to maintain safety. The future is only brighter with multiple new systems being tested to assure high levels of reliability and longevity.