DALLAS — In contemporary aviation, passenger-to-freighter (P2F) conversions represent a tested strategy to meet the increasing needs of global air cargo. Although the idea is not new, its relevance has never been greater.
With e-commerce and time-sensitive logistics revolutionizing the sector, the conversion of existing passenger planes presents airlines with an efficient means to expand operations rapidly, economically, and sustainably. Rather than investing in costly new aircraft, operators convert proven airframes for freight operations, balancing flexibility with cost control in an environment where speed and flexibility are highly regarded.
According to Boeing's 2024 World Air Cargo Forecast, the world freighter fleet will need more than 2,800 aircraft by 2043, of which over 50% would be from passenger conversion. Knowing the complex, highly engineered process of P2F conversions is essential as airlines look for cost-effective solutions to meet global freight demand.
The Rationale Behind P2F Conversions
Several strong reasons motivate the conversion of a passenger aircraft into a freighter:
- Cost Efficiency: Converting a passenger aircraft to a freighter is much more cost-effective than acquiring a new-build freighter. The converted aircraft are usually possessed or purchased at significantly lower market value. This reduces the high capital cost of brand-new aircraft, which can be burdensome to operators. Also, converted freighters avoid the long wait times typical of new aircraft production, allowing for more rapid fleet growth without new production's financial and logistical costs.
- Extended Life: Conversions give new life to airframes that might otherwise be retired, extending their useful life by several more years (15–20 years). This maximizes return on investment in the aircraft and enables airlines to postpone the very high costs of fleet renewal.
- Quick Deployment: Unlike new freighters, which take years to deliver because of scarce production slots, P2F conversions are done in a short period, typically months. It is essential for carriers that wish to respond swiftly to surges in freight demand, especially in rapidly developing markets or during supply chain breakdowns globally.
- Environmental Advantages: Recycling plane frames into cargo planes minimizes industrial waste and carbon emissions compared to new production.
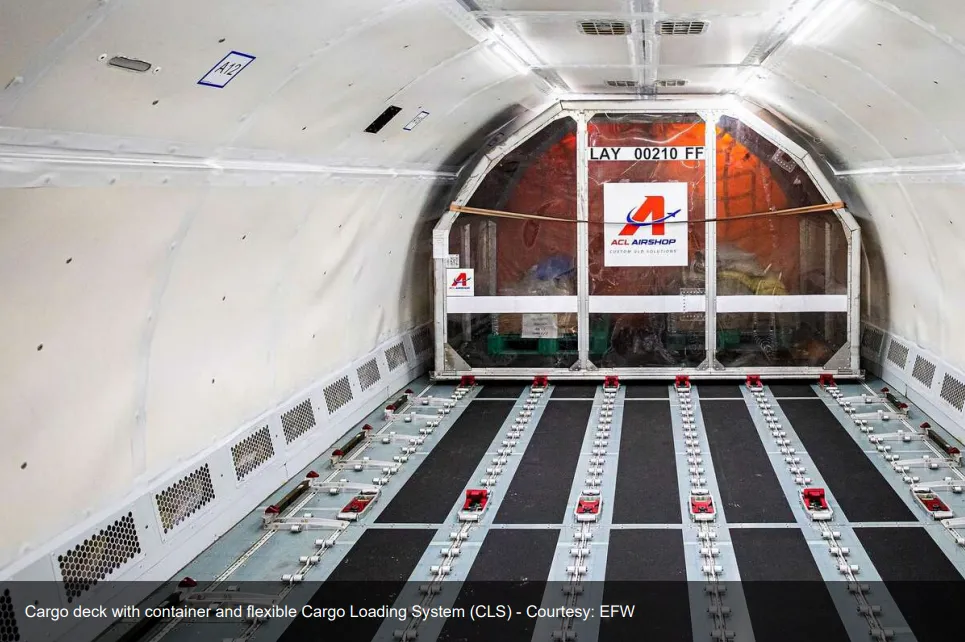
The Step-by-Step Conversion Process
Passenger-to-freighter conversion is a critical multi-stage procedure with structural, mechanical, and regulatory nuances.
- Selection of Aircraft and Viability
Not every passenger airliner is the best candidate to be converted to a freighter. Engineers judge structural health, maintenance record, and suitability to the cargo marketplace. Narrow and mid-size widebody models such as the Boeing 737-800, 767- 300ER, and Airbus A321 are regularly selected because of their availability and well-balanced cargo capacity. Older aircraft made of aluminum are preferred since these can be easier to structurally modify compared to newer composite-centric models such as the A350, which is more complicated and expensive to reconfigure.
- Stripping and Disassembly
The conversion process starts with removing all elements of the passenger cabin, such as seats, galleys, lavatories, overhead bins, and insulation. The windows are plugged or strengthened, and the cabin is stripped for the fuselage exposure for modification. This is essential in weight reduction and preparing the structure for reinforcements and cargo system fittings. Disassembly is economical, offering a practical path to extend aircraft life. This initial stripping typically takes 2–3 weeks, depending on aircraft complexity.
- Structural Modifications
Structural additions are essential for supporting the more concentrated loads of freight pallets:
- Floor beams are reinforced, and new roller tracks are fitted.
- Main cargo doors are trimmed and framed into the fuselage. For instance:
- Boeing 737-800BCF: Door size around 141 x 86 inches.
- Boeing 777-300ERSF: Larger door at 106 x 67 inches.
These changes must comply with FAA/EASA certification requirements through a Supplemental Type Certificate (STC).
- Systems Upgrades
Freighters have different operational mechanisms from passenger jets:
- Avionics enhancements provide navigation and environmental monitoring functions to freight operations.
- The hydraulic system is diverted to operate the new equipped cargo doors.
- Fire protection systems are fitted in the cargo hold, as an ICAO safety requirement.
- Interior Reconfiguration
Following the structural alterations, the aircraft interior is rearranged:
- Roller systems and ball mats are provided to facilitate ULD mobility.
- Nets and solid barriers hold freight during turbulence.
A 737-800BCF will carry 11–12 pallets, whereas a 747-400BCF will carry 30–34 pallets, illustrating a dramatic capacity disparity based on platform size.
- Testing and Certification
Before a converted freighter is allowed into commercial service, it must undergo intense ground and flight testing. These tests verify that all the structural changes, including reinforced flooring, cargo doors, and modernized systems, are up to safety and performance standards. Everything from cargo loading systems to avionics and emergency procedures is tested. Once all systems are validated, an aircraft may be granted a Supplemental Type Certificate (STC) by regulatory bodies such as the FAA or EASA. This allows the aircraft to be officially recognized as airworthy as a freighter and compliant with international aviation safety standards.
- Painting and Delivery
After successful certification, the freighter is repainted, usually in the operator's livery, and readied for commercial freight service. On average, the conversion process from induction to redelivery takes 100–130 days.
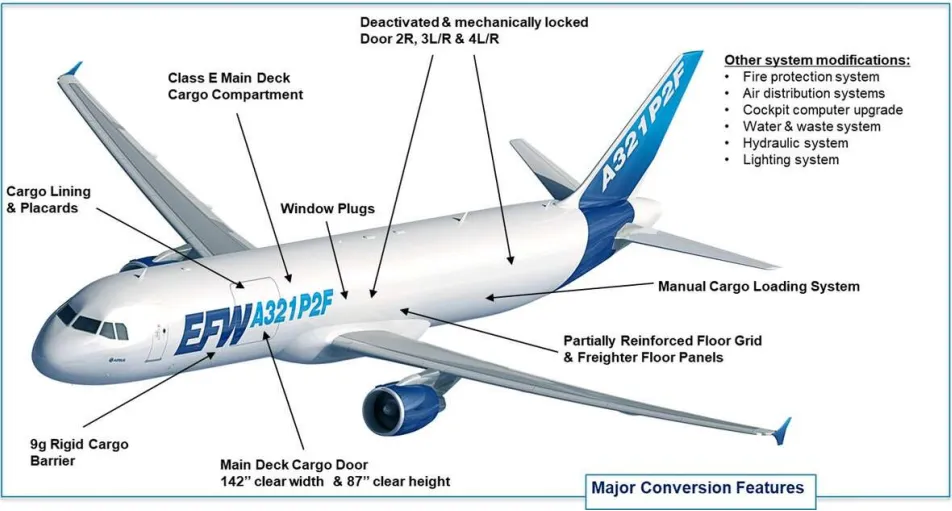
Case Study: The Boeing 777-300ERSF "Big Twin"
A breakthrough in freighter conversions, the Boeing 777-300ERSF, which was designed by Israel Aerospace Industries (IAI) and GECAS, offers:
- Payload: 100 tonnes
- Cargo Capacity: 820 m³
- Fuel Efficiency: 21% less fuel consumed per tonne than 747-400 freighters
With more than 95% commonality with the 777-passenger fleet, the Big Twin offers lower costs and easier fleet integration for carriers such as Kalitta Air, a launch customer. The Boeing 777-300ER is one of the latest airframes to retire from passenger service, so it is a good time for freighter conversions.
Israel Aerospace Industries (IAI) is the first to be certified to convert the 777 into a freighter. The 777-300ERSF offers significant benefits: it carries 25% more payload capacity than the factory-new 777F at a payload of 101.6 tonnes, and uses up to 20% less fuel than the 747 freighter.
One of the oldest operating converted freighters is a Boeing 707-320C model, restored in the late 1960s. Airlines such as Flying Tigers and Pan Am were the first to pioneer early conversions, manually reinforcing floors and doors without today's computer-aided designs.
Contemporary conversions are much safer, lighter, and quicker, demonstrating half a century of technological progress.
Why Boeing, Airbus Still Manufacture Freighters
Despite P2F successes, Original Equipment Manufacturers (OEMs) such as Airbus and Boeing are still producing new freighters. New builds such as the 777-8F provide:
- Higher payload (118 tonnes)
- Optimized cargo floor space
- Integrated modern engine and avionics technology
Operators who require the newest environmental standards and optimum fuel economy, which are most important for intercontinental missions, also favor new constructions.
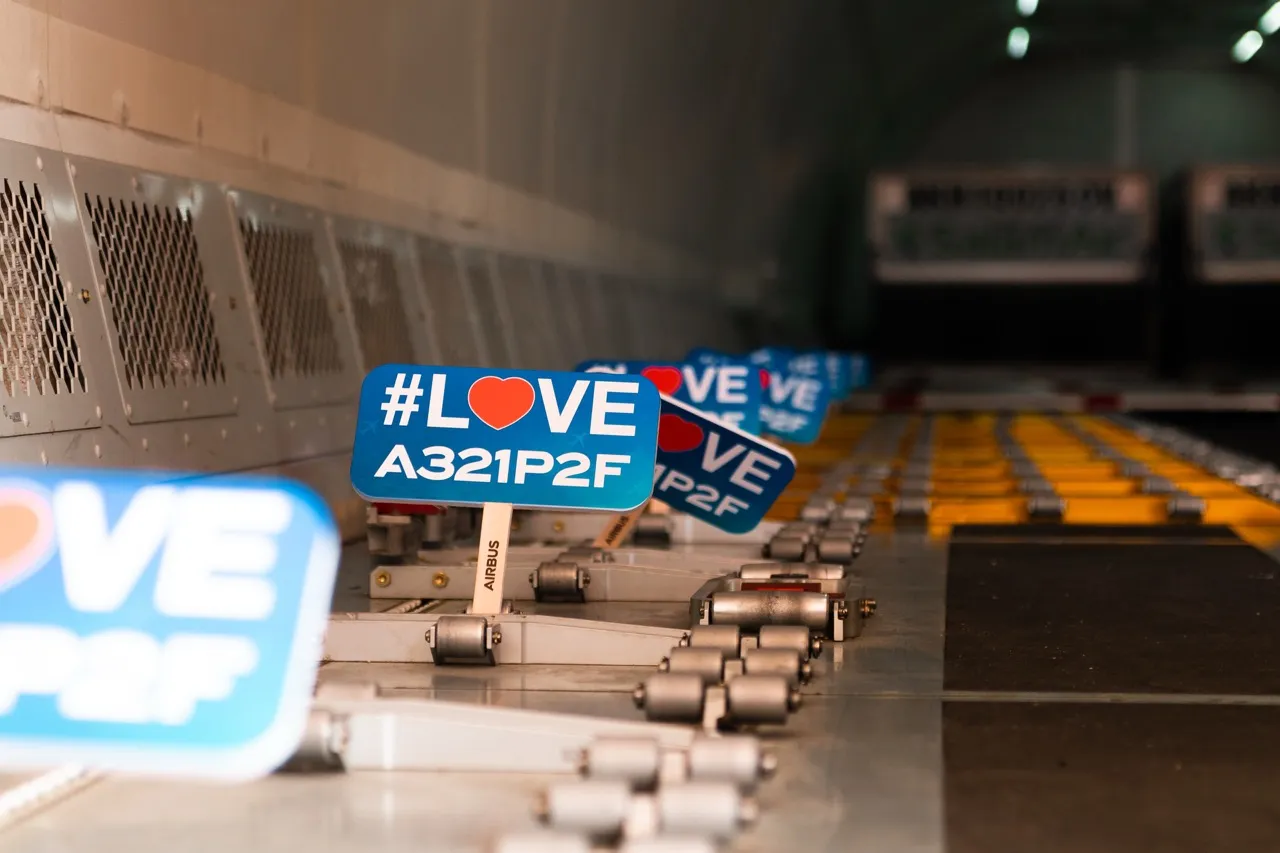
Cost Differences: New vs Converted Freighters
Conversions represent a quicker, lower-cost route to freight operations for airlines, while new aircraft have a longer-term benefit in operating efficiency and emissions compliance. Global Air Freight's Future, law firm Reed Smith reported in 2022, quoting IBA statistics, of the significant capital required for freighter conversions.
According to the report, it takes around US$4.2 million to convert a narrowbody plane like the Boeing 737-800, and an Airbus A321-200 conversion is around US$6.1 million. The amount is much higher for widebodies: around US$14.7 million for a Boeing 767-300ER and US$18.4 million for an Airbus A330-300. As the report points out, these numbers illustrate the high conversion costs.
Engines Upgrades, Using P2F-converted Aircraft
Engines are usually not replaced in P2F conversions unless they approach service life thresholds. Minor overhauls are done to maintain reliability, but the original engine models, such as the GE90s on 777s or CF6s on 767s, are kept. Engine maintenance cost planning becomes essential for operators after conversion.
Freighter conversions offer significant cost advantages over new builds. Converting existing passenger aircraft into freighters is usually more cost-effective than purchasing brand-new freighters, allowing operators to rapidly increase their cargo capacity and with less initial outlay.
As of early 2025, more than 2,000 converted freighters are active in service worldwide, with hundreds more on order. E-commerce growth, especially in Asia-Pacific and emerging markets, keeps driving the expansion.
With Boeing ceasing 767F production by 2027 and the 747-400Fs approaching retirement, the P2F market is set for continued growth, particularly in the widebody market.
Technological innovations like intelligent cargo tracking, lighter-weight composite materials, and automated loading systems will also define the future of the freighter conversion business.
Conclusion
The passenger-to-freighter (P2F) industry remains a progressive strategic cornerstone within the aviation world's reaction to changing global supply chains. Going beyond the bottom-line attraction, conversions are an indispensable means of helping to meet the capacity gaps produced by slow-rollout new-build freighter orders and faster fleet retirements.
Enhancing structures, protection systems, and STC protocols has streamlined return-to-service timings and made the conversion process more efficient. Asia-Pacific, Middle Eastern, and Latin American markets are developing conversion pipelines to address regional freight spikes, underpinned by localized MRO capabilities and growing e-commerce volumes.
Strategic collaborations between lessors, OEMs, and MRO suppliers like IAI with GECAS and Airbus with EFW are also transforming the rate at which converted freighters are introduced to the market. As regulatory requirements and carbon efficiency become more stringent, operators are likely to consider P2F increasingly as both a short-term fix and a long-term solution to fleet renewal with sustainability at its core.