DALLAS — Almost all aircraft cabins are air-conditioned and pressurized to ensure passenger comfort during flights at high altitudes. Outside the aircraft at cruising altitude, the temperature is cold enough to drop to -60°C, and the air pressure is too low to support human life.
A complex air conditioning system is employed not just for comfort heating or cooling but also for providing ventilation, pressurization, and humidity control onboard.
Current turboprop and turbofan aircraft utilize environmental control systems using conditioned air. While the fundamental equipment utilized in each aircraft configuration remains the same, the air supply source, system configuration, and level of automation vary depending on the engine configuration.
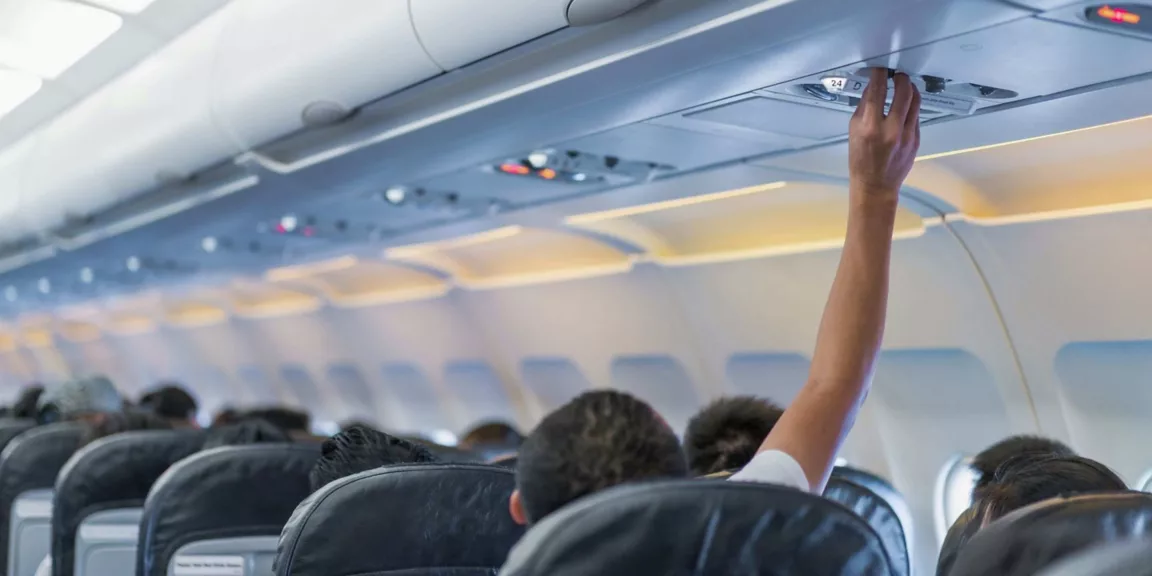
Air Conditioning Systems in Turboprops
Turboprop engines are likely to use vapor-cycle air conditioning systems. These are similar to those used in ground vehicles, utilizing a refrigerant coolant that circulates rather than the engine bleed air found onboard turbine-powered jets.
The principal components of a turboprop's vapor-cycle system include a refrigerant compressor, condenser, receiver-dryer, expansion valve, evaporator, and air flow fans. Tetrafluoroethane (R134a) is the most prevalent refrigerant used in most systems due to its environmental compatibility.
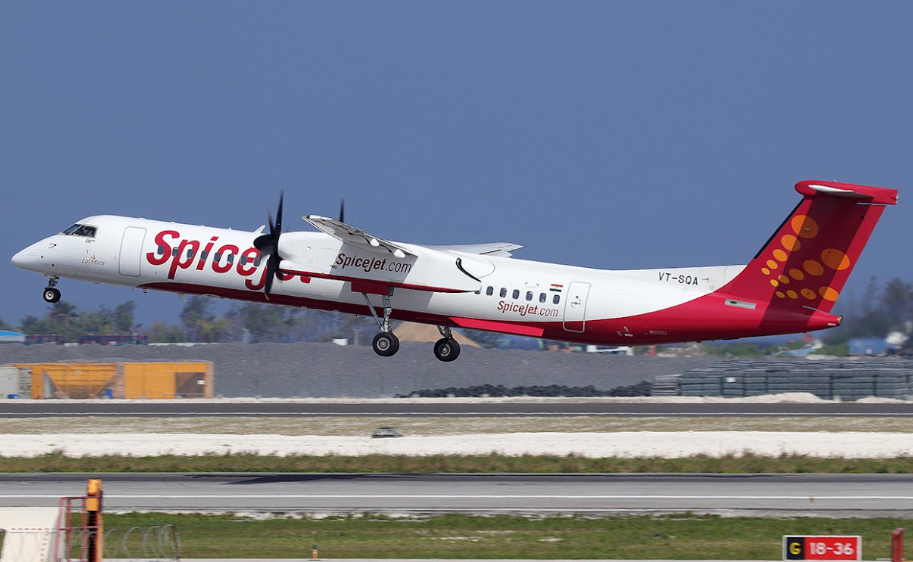
Working Principle of the System
- Compression: The gas is compressed, resulting in an increase in its temperature and pressure.
- Condensation: The outside air cools the high-pressure hot refrigerant in the condenser, causing it to turn into a high-pressure liquid.
- Expansion and Cooling: It is subsequently cooled through an expansion valve, which lowers pressure and temperature before it is supplied to the evaporator.
- Heat Absorption: As cabin air flows over evaporator coils, heat is absorbed, and the refrigerant evaporates, thereby cooling the air.
- Air Delivery: The cool air is subsequently delivered into the cabin.
An electric motor or an engine can power the compressor. Electric compressors are less site-specific and are being increasingly utilized in newer turboprops to a greater degree. Although vapor-cycle systems are used in small to medium-sized aircraft, they cannot be utilized in large jets. That is where air-cycle systems are employed, in turbofan-powered airliners.
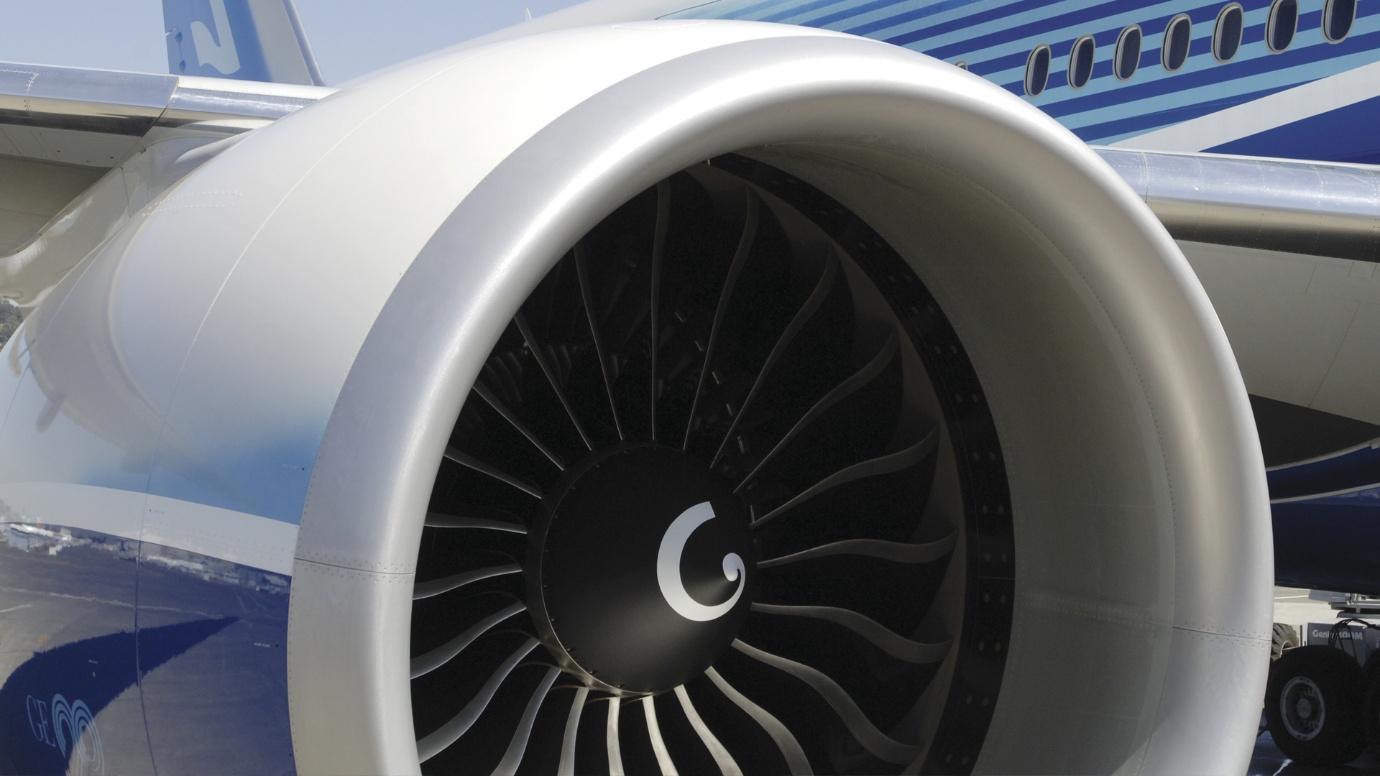
Air Conditioning of Turbofan Aircraft
Turbofan aircraft utilize bleed air from the engines as the primary source of their air pressurization and air conditioning. This hot, high-pressure air is suctioned from the compressor section of the engine and subsequently processed through an air cycle machine (ACM).
The air cycle system can also be referred to as a "PACK" (Pneumatic Air Conditioning Kit). The two or more packs that are found on most large jets, such as the Airbus A320, Boeing 737, and 777 series, are located near the main landing gear area.
Air Conditioning PACK Major Parts:
- Pack Valve (FCSOV): Regulates the quantity of bleed air fed to the system.
- Primary and Secondary Heat Exchangers: Use ram air to cool hot bleed air in a staged process.
- ACM (Air Cycle Machine): Has a compressor, turbine, and occasionally a fan, all on a shared shaft. The machine does not use any refrigerant.
- Reheater and Condenser: Maximize cooling through heat exchange between various airflow streams.
- Spray Nozzle and Water Extractor: Dry chilled air and re-use it to optimize heat exchanger efficiency.
General Overview of the PACK Operation:
- Air Supply: Bleed air from the engine or APU is supplied to the primary heat exchanger and partially cooled by ram air.
- Compression and Cooling: It is compressed within the ACM, causing it to warm up again. The second heat exchanger then sheds this heat with the assistance of additional ram air.
- Expansion and Moisture Removal: Air then expands through the turbine, chilling significantly. It passes through the condenser and water extractor, removing humidity.
- Blending and Distribution: Cold, dry air is mixed with bypass hot bleed air to achieve the desired cabin temperature before being distributed through ducts.
The system is self-sustaining and efficient, and uses no refrigerant. It also helps reduce aircraft weight and maintenance complexity and is ideal for long-range and high-capacity operations.
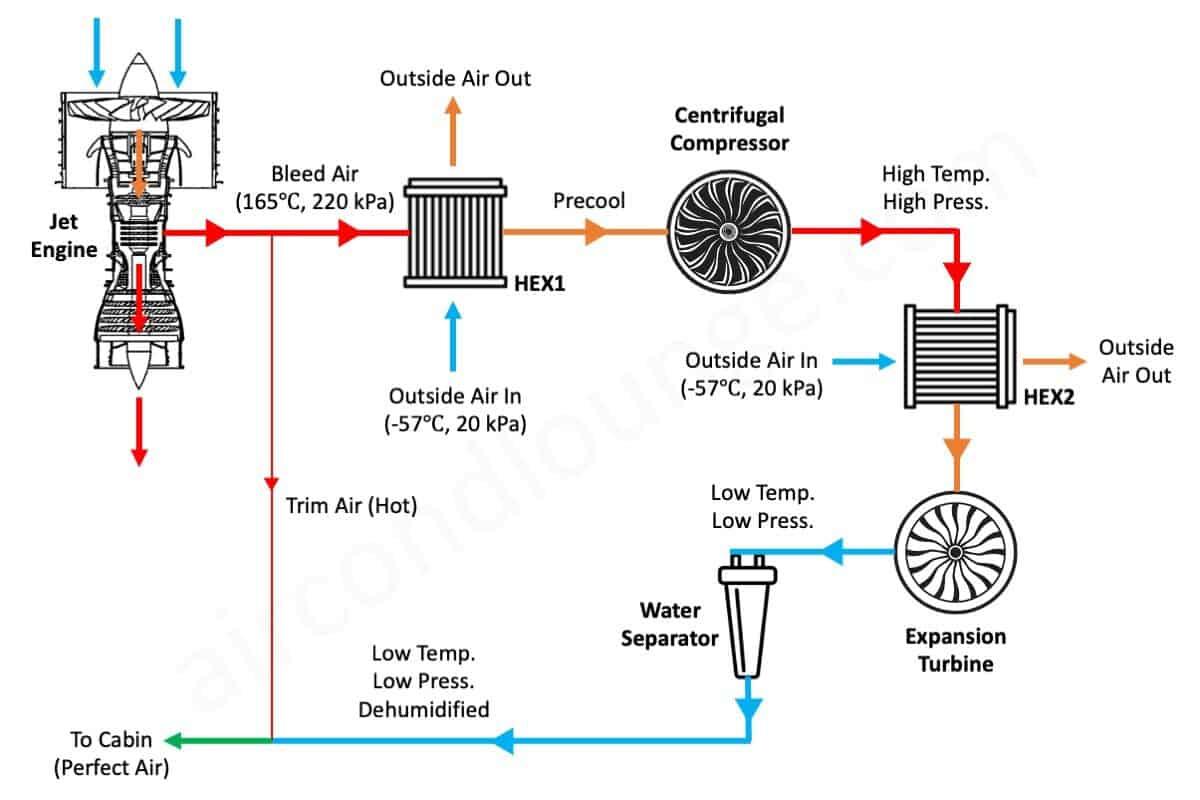
Differences Between Turboprop, Turbofan AC Systems
- Air Source:
- Turboprops utilize atmospheric air cooled through refrigerant cycles.
- Turbofans use engine (compressor) bleed air and air cycle equipment.
- Cooling Method:
- Turboprop engines incorporate chemical cooling with refrigerants such as R134a.
- Turbofans utilize physical expansion and ram air cooling, eliminating the need for chemicals.
- System Complexity:
- Fewer moving parts are present in turboprop's simpler systems.
- Turbofans possess advanced PACK systems with multi-stage redundancy for safety.
- Power Source:
- In turboprops, the compressor may be engine-belt-driven or electric.
- The pneumatic pressure from bleed air powers the turbofan system.
- Scalability:
- Vapor cycle systems are appropriate for small and light-weight aircraft that do not require pressurization.
- Air cycle systems may be designed for high-altitude, large aircraft with intricate cabin zoning.
Cabin Air Quality, Recirculation
On both aircraft, maintaining a clean and fresh air environment is a necessity. About 50% is recirculated, with the other half being fresh. The recirculated air passes through High-Efficiency Particulate Air (HEPA) filters, which can trap up to 99.999% of airborne viruses and bacteria. This configuration is standard in turbofan jets and is also found in more and more newer turboprops.
Cabin temperature is sensed and regulated by the flight crew through temperature control panels that receive their inputs from sensors located across various zones. When the temperatures exceed safe limits, overheat switches execute system shutdowns and warnings.
The trim air system provides very accurate control by adding small amounts of hot bleed air to the conditioned flow. These valves are commonly referred to as Mixing Valves, Trim Air Valves, or Temperature Control Valves by different manufacturers.
Special Case: Boeing 787 Bleed-less System
The Boeing 787 Dreamliner differs from conventional air supply systems in that it has a bleed-less system. It does not take in hot air from engines, but instead takes in clean air from the environment through electrically powered cabin air compressors (CACs). This has the effect of decreasing engine load and increasing fuel efficiency.
The CACs compress filtered, cooled, and humidified ambient air. The system is humidity-controlled based on the passenger numbers entered by the crew. Approximately 50% of the cabin air is recirculated after passing through a HEPA filter for both hygiene and energy benefits. This is an introduction to electricity-based environmental control systems for next-generation aircraft.
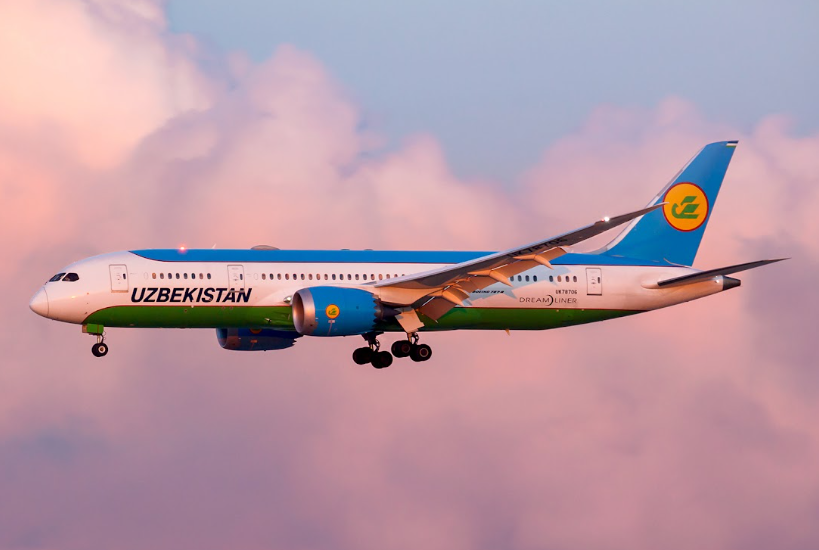
Ground Operations, Environmental Factors
When the aircraft is at the gate, the engines are shut off. It is in this case that the APU supplies pneumatic and electrical power to run the air conditioning system. If the APU is not operating, passengers will notice a delay in cabin cooling.
Alternatively, airports supply pre-conditioned ground air through external hoses, reducing the need to run APUs and emissions. Post-boarding, ground air is cut off, and the APU powers until engine start. Air conditioning is also used to supply heat. During winter, the same system augments bleed air mixing to heat the cabin. This dual-capacity function allows aircraft systems to be beneficial over a range of temperatures.
Conclusion
Although the ultimate application of an air conditioning system is to create a safe and comfortable environment for travelers aboard various categories of aircraft, the process differs significantly for turboprops and turbofans. Turboprops utilize vapor-cycle refrigerant systems, which are suitable for small cabins, while turbofan jets employ advanced air-cycle PACKs with bleed air and ram air cooling.
The advent of bleed-less systems such as the Boeing 787 is a trend toward electrically powered air conditioning with reduced engine dependencies. As aircraft become increasingly advanced, so do environmental control systems become more intelligent, efficient, and responsive to the needs of passengers, while continuing to ensure the safety and reliability that aviation requires at 35,000 feet.